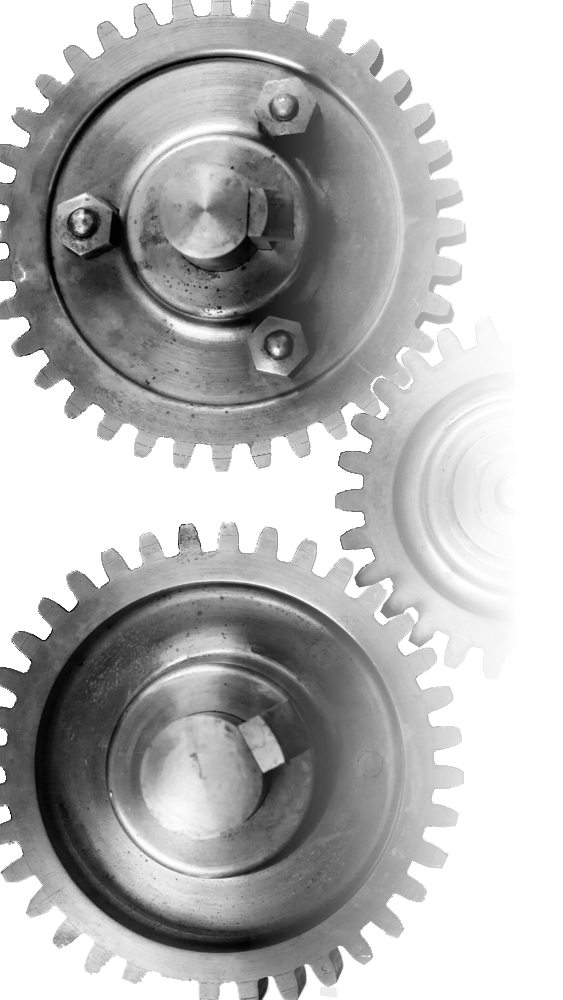
Every training module is unique, and serves the purposes of the operator trainees as each mill site requests. All training modules need to accomplish several goals:
Process Module Goals
- Address needs of off-the-street new hires as well as experienced/lateral moving operators.
- Address needs of governance and updating with limited mill resources. SOP reviews occur every year or two, training module reviews occur every 2-5 years.
- A corollary of governance and updating has led us to develop a simple but still visually appealing design. The modules are arranged with a full page text and accompanying full page graphic to keep it simple.
- Keep modern readers engaged in a static format.
- We have deep experience in the development of multimedia “video-style” training modules. Multimedia is by far the most engaging way to show process concepts. However, it is frightfully expensive (3x – 8x the cost for similar coverage to a paper-based module), takes a long time to develop, and cannot be easily updated by mill resources.
- Paper-based, computer-delivered process modules act as a bridge between expensive but generic multimedia presentations and detailed field tasks documented by cheap SOPs. A paper-based module format is the obvious choice from an updating perspective. Mill process changes and improvements are constant, and the training documentation has to reflect those changes. To get the most out of a paper-based format for younger visually-oriented audiences, we produce high quality illustrations that both simplify process flows & technical points, while keeping readers engaged.
Process Module Typical Coverage
In addition to these broad goals, the content of training modules for a process system of input streams and output streams that are reacted or physically processed, have some broad categories of information that an operator almost always needs to know. These categories include:
- System or Process Overview
- System Components
- Process Flows
- Process Controls & Instrumentation
- Operational Concerns (added detail as available)
These categories are not airtight. Many industrial systems don’t fit these categories, including woodyard operation, electrical generator, electrical substation operation, many elements of steam turbine operation, conveyor and converting systems, box making mechanical equipment, corrugation equipment, etc. These don’t have traditional chemical and material process flows. Working with experienced consultants can help deciding the best approach to take for a particular system.
For a flavor of how the coverage might shake out for a process system, click the button below to see some introductory pages for a cooling tower system.